Nun ist mein Eigenbau der Vendee Mirage 2000 seit fast schon neun Jahren im Einsatz. In dieser Zeit hat sie einiges mitmachen müssen. Nicht nur, dass ich schon mehrmals das Fahrwerk erfolgreich in der Luft ausgebaut habe, auch die Turbine hat schon mehrere »wet starts« und Feuer über sich ergehen lassen. Nun wurde es Zeit, eine neue Mirage zu laminieren und aufzubauen. Äußerlich sollte sich die neue Mirage von der bisherigen nur in Detaillösungen unterscheiden. Da ich in den letzten Jahren auch laminiertechnisch einiges dazugelernt habe, war mein Ziel, bei gleicher Steifigkeit einige Kilos zu sparen.
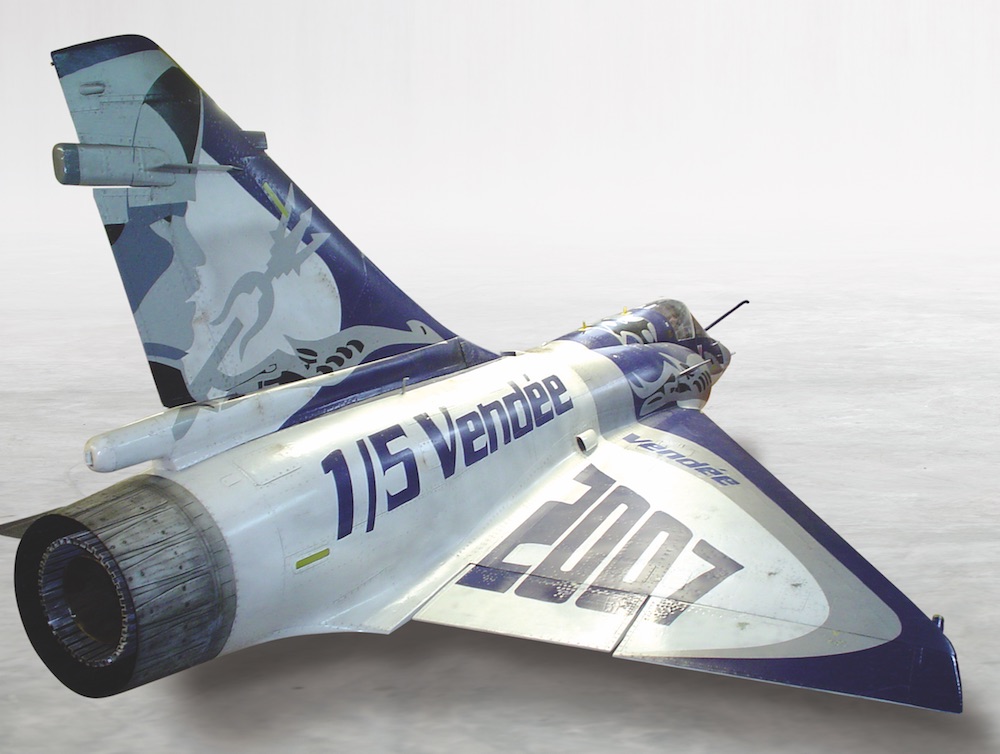
Bei der alten Mirage wurde der Rumpf noch im Sandwich gebaut, diesmal laminierte ich sie aber nass in nass, dazu aber später mehr. Ich kramte die über 60 Formteile aus dem Lager und begann mit dem Wachsen. Um Gewicht und unnötige Arbeit zu sparen, lackierte ich die Formen mit Grundierung. Die Teile waren nicht wie bei herkömmlichen Bausätzen weiß oder silber, sondern beige. Das störte mich aber nicht weiter. Zuerst laminierte ich die ganzen Kleinteile wie die Finnen, Wartungsdeckel, Cockpitteile usw. Da die Teile wie gesagt nass in nass laminiert wurden, ging das schnell von der Hand. Ziel war es, möglichst leicht zu werden und trotzdem stabile Teile zu erhalten. Um dies zu schaffen, verwendete ich dünne Depron-Streifen, um den Hohlraum zwischen den beiden Formenhälften zu füllen. So wurden z. B. der Tankrüssel und die Finne laminiert. Da reichte oft schon eine einzige Lage 50 g / mm² als Außenlage.
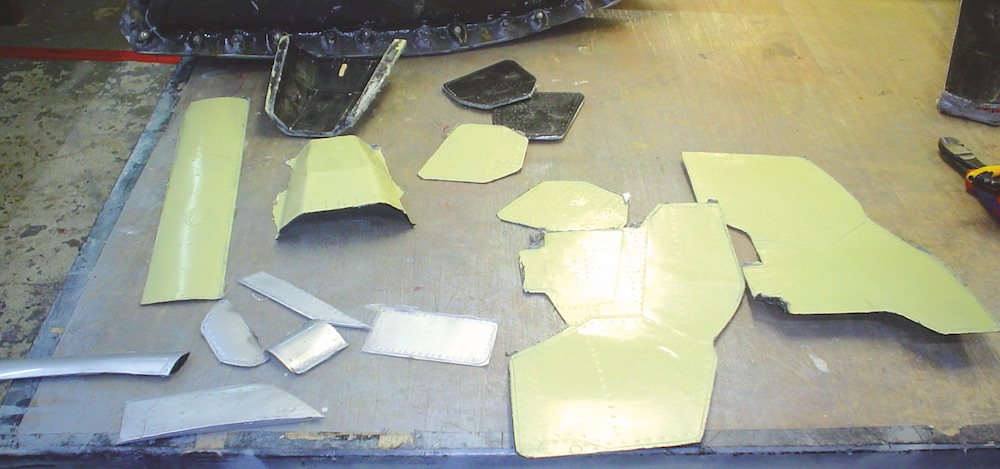
Für die Cockpitteile wie den Schleudersitz habe ich Silikonformen. Da so ein Schleudersitz einige Hinterschneidungen hat, lässt sich das Bauteil so später einfacher entformen. Auch ein Wachsen ist bei Silikonformen unnötig. Ich benutze dazu die Produkte von HP Textiles und bin damit sehr zufrieden. Um in die verwinkelten Formen blasenfrei laminieren zu können, schnitt ich kleine Gewebereste zurecht und tupfte sie in alle Ecken der Formen. Fahrwerksdeckel, Air Inlet usw. mussten in Sandwich laminiert werden, um leichte Teile bei hoher Festigkeit zu bekommen. Als Stützstoff benutze ich 2 mm starkes Airex. Zusätzlich zum GfK-Gewebe wurden besonders beanspruchte Stellen mit Kohlefaser Gewebe verstärkt.
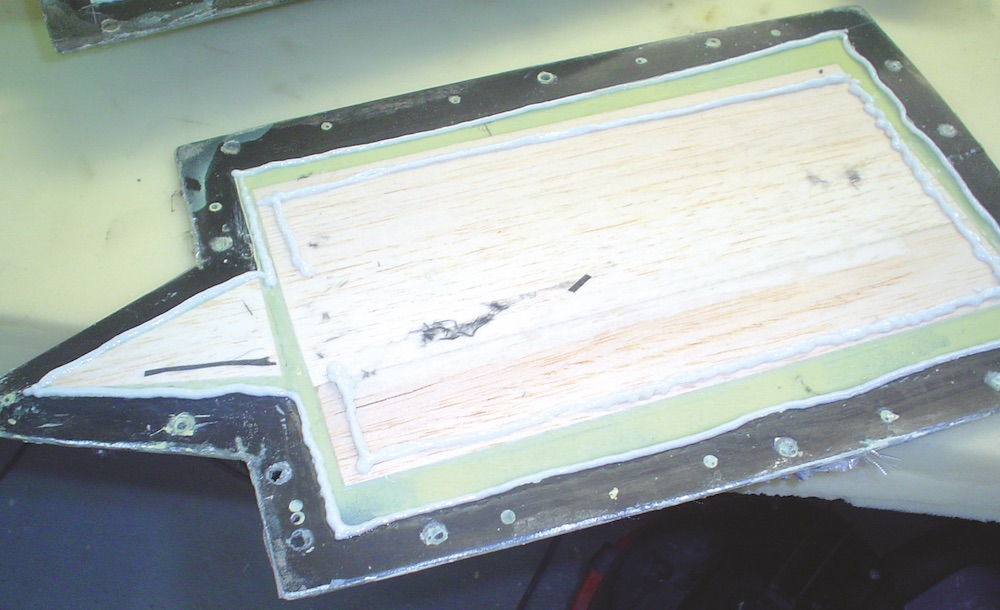
Die Ruder wurden ebenfalls in Sandwich hergestellt. Als Außenlage reichte ein 50 g / m² GfK-Gewebe locker aus. Nach dem Stützstoff kam wieder eine 50 g-Matte rein. Nur an der Scharnieraufnahme wurde zusätzlich mit einem dünnen Streifen Kohlefaser verstärkt. Die Scharniere bestehen aus einem 2 mm-Stahldraht in einem Kunststoffrohr. Diese wurden vor dem Zusammenkleben der beiden Formenhälften genau an der Drehachse des Ruders eingelegt und verklebt. Das Gewicht war unschlagbar.
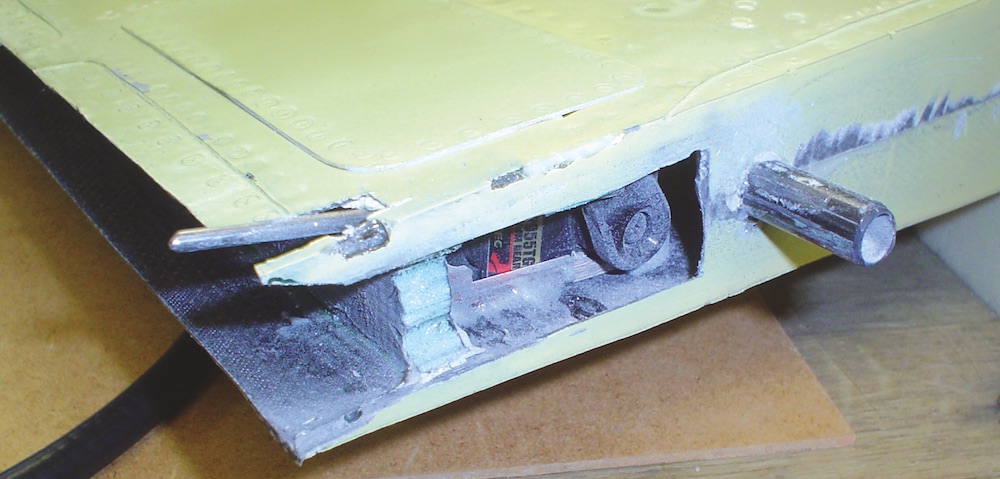
Bei Tragfläche, Turbinendeckel und Seitenruder versuchte ich etwas neues. Als Stützstoff benutzte ich nicht das altbewährte Airex, sondern einen 2 mm starken Polystyrol-Schaum. Das Zeug ließ sich sehr leicht um Ecken biegen und das Gewebe haftet besser. Der Schaum ist aber sehr empfindlich gegenüber Temperatur und aggressiven Flüssigkeiten. Daher ist es nur an Teilen zu verwendet, die nicht direkt im heißen Bereich der Turbine liegen. 50 g-GfK als Tragflächen-Außenlage war für mich dann doch etwas zu wenig. Wobei vermutlich dieses Gewebe locker im Flug reichen würde. Aber die Mirage sollte alltagstauglich und nicht nur mit Samthandschuhen zu transportieren sein. Also baute ich den Flügel mit einer Lage 50 g und einer Lage 80 g, dann Stützstoff und schließlich nochmal 50 g-Gewebe auf.
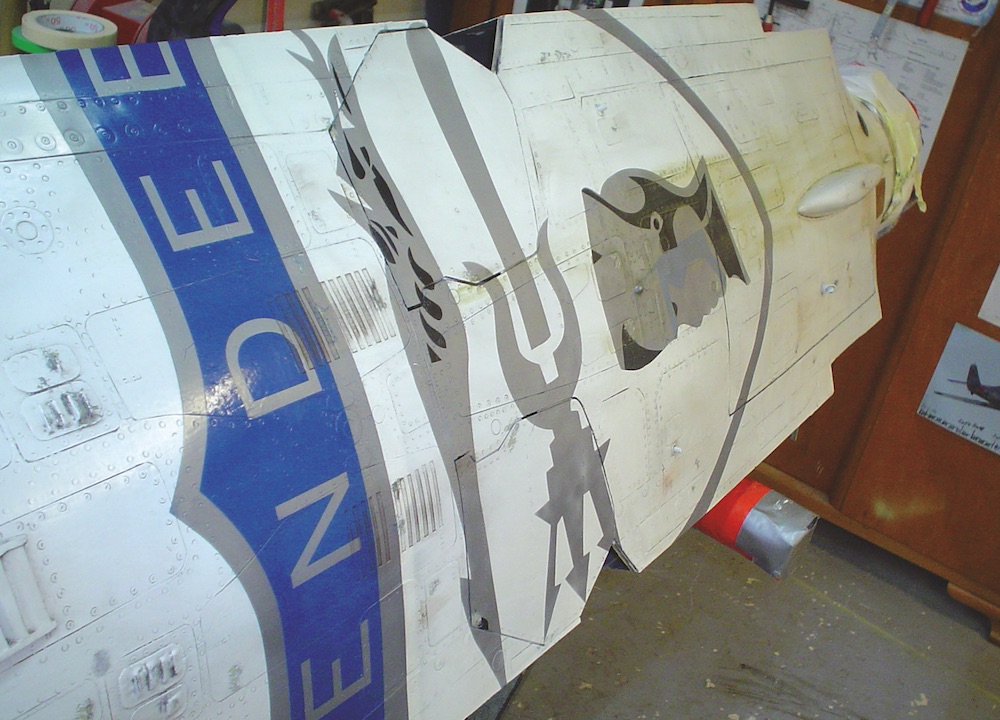
Um G-Kräfte und Fahrwerks-Schläge gut einleiten zu können, wurde großflächig Kohlegewebe verlegt. Rippen und Fahrwerksaufnahme bestehen aus Kohle-beschichteten Pappel- und Flugzeug-Sperrholz. Ein Vorteil beim selbst laminieren ist, dass man Servos und Kabel vor dem Zusammenkleben der Formenhälften an ihrer Position befestigen kann. Dies spart Zeit und Nerven … Als Flügel-Arretierungen dienen drei 10 mm-Kohlerohre und zur Befestigung an den Rumpf drei M4-Einschlagmuttern. Etwas tricky war das Positionieren der Fahrwerksaufnahme. Die Mirage hat nämlich angewinkelte Fahrwerksbeine und fährt diese schräg nach vorne ein.
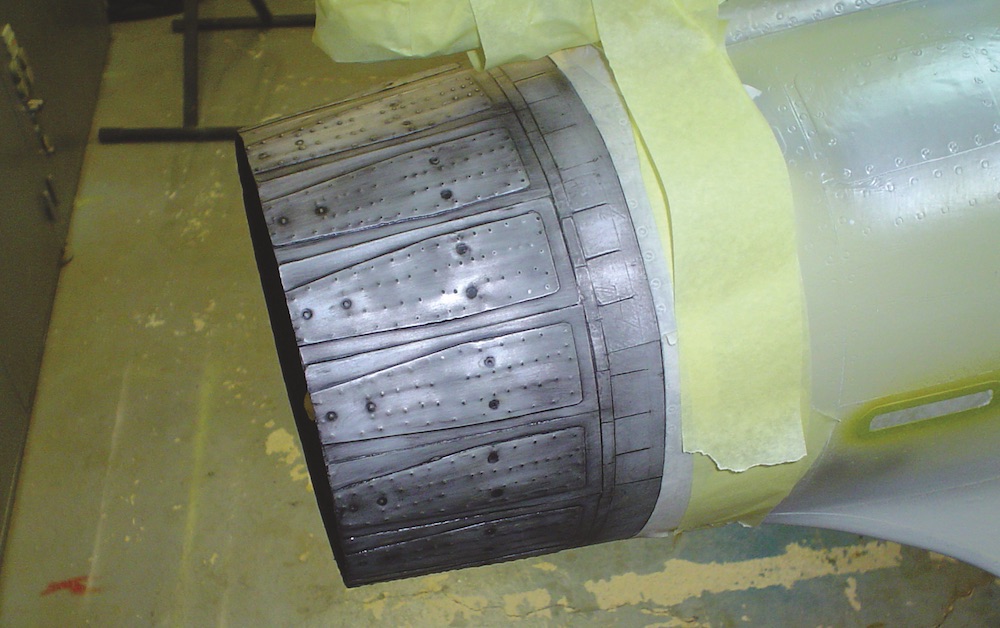
War der Rumpf des Vorgängermodells noch in Sandwich konstruiert, sollte er nun nass in nass aufgebaut werden. Ziel war, leicht und trotzdem stabil genug zu werden. Auch hier verwendete ich Kohlefaser-beschichtete Pappelsperrholz-Spanten, um den an Gewebe gesparten Rumpf leicht und steif genug zu bekommen. Den Rumpf baute ich wie folgt auf: Eine Lage 25 g / m²-GfK für eine perfekte Oberfläche, dann eine Lage 50 g-GfK, und …