Die Landshut entsteht
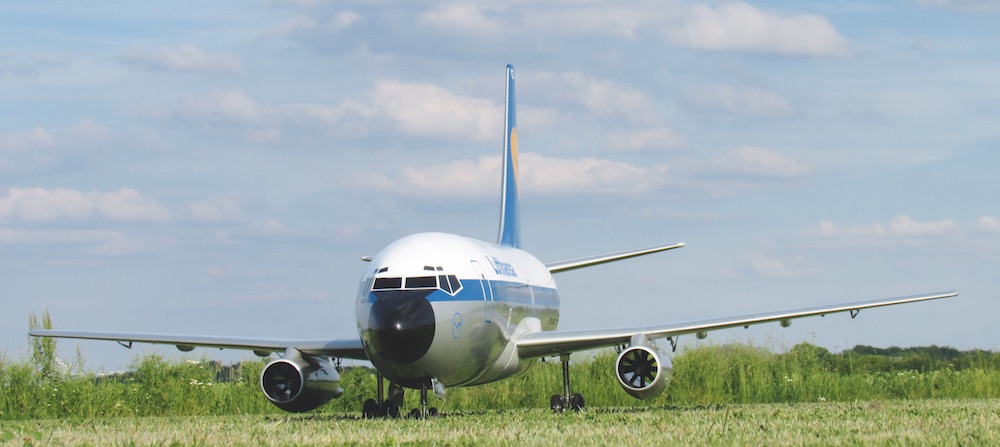
Eigentlich den etwas größeren Airlinern mit Turbinenantrieb zugetan, habe ich seit etwa drei Jahren auch die Vorteile eines kleineren Modells mit Elektroantrieb zu schätzen gelernt. Ein Nachbau der eleganten französischen Caravelle war entstanden, ausgestattet mit zwei 70 mm E-Impellern, gespeist durch einen 6s LiPo. Der geringe Aufwand für Transport, Auf- und Abbau am Platz sowie das unkomplizierte Handling stellten eine willkommene Alternative zu den großen Jets dar. Nun hat mittlerweile der eigene Nachwuchs zunehmend Gefallen an der Caravelle gefunden und ich komme kaum noch dazu, sie selbst zu fliegen. Was tun?
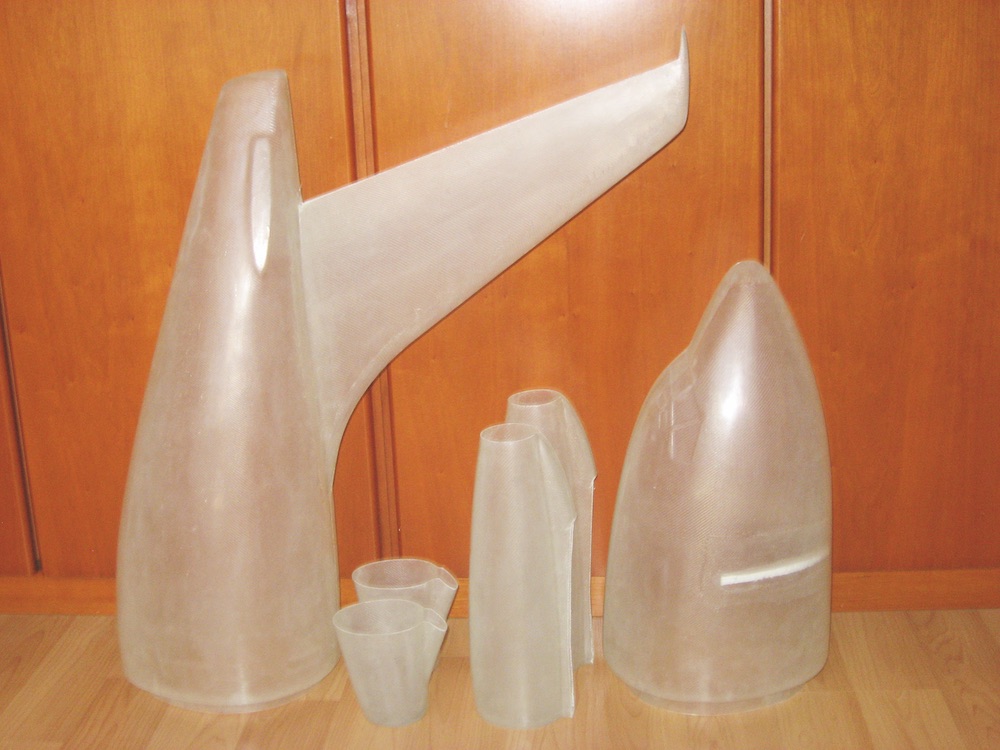
Ein kleiner Rückblick: Vor einigen Jahrzehnten hatte ich damit begonnen, Negativformen zur Herstellung wesentlicher Komponenten für den Bau von Airlinermodellen zu erstellen. Konkret hieß dies, dass Rumpfnase und Rumpfheck mit Seitenleitwerk sowie die Triebwerksgondeln in GfK-Technik angefertigt werden konnten. Auf diese Weise waren damals Formen unter anderem für die Boeing 737 in den seinerzeit aktuellen Versionen 737-100 und -200 entstanden. Mein um 1977 / 78 entstandenes Modell einer 737-200 wurde mit zwei 6,5 cm³-Zweitaktern motorisiert, der einzigen Antriebsmöglichkeit zur damaligen Zeit. Die notwendige Bodenfreiheit für die Luftschrauben machte ein extrem hochbeiniges Fahrwerk erforderlich, das allein schon deshalb nicht einziehbar sein konnte, weil die langen Beine beim Einklappen nach innen miteinander in Konflikt gekommen wären. Abgesehen von diesem optischen Mangel flog das Modell ganz gut, mal abgesehen von dem überaus kritischen Verhalten bei einseitigem Motorausfall.
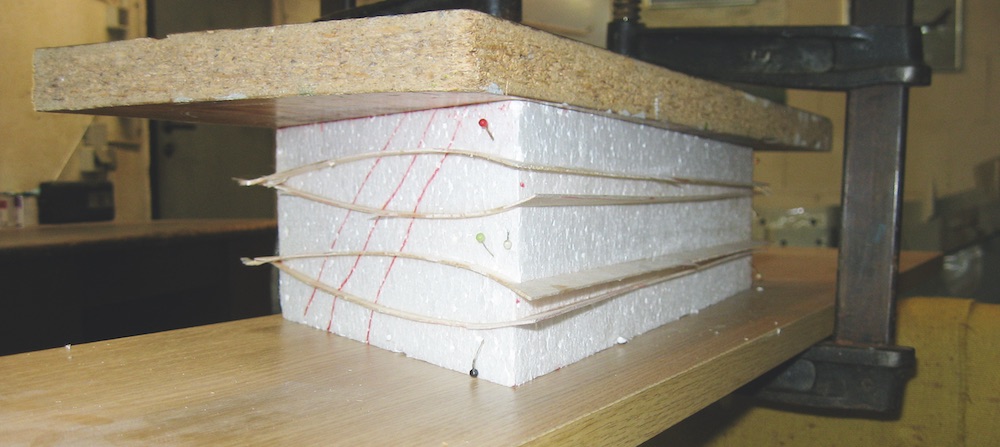
Heutzutage sind die Möglichkeiten ganz anders. Die Verwendung von Impellern macht ein vorbildgetreues niedriges Fahrwerk möglich, wie es für die 737 gerade so typisch ist. Mit der Verwendung von Elektroantrieben ist auch die Wahrscheinlichkeit eines einseitigen Motorausfalls deutlich gesunken. Und sollte es trotzdem einmal dazu kommen, kann der Einbau eines Dreiachs-Kreisels dieser Situation zumindest etwas von ihrer Dramatik nehmen. In die langen schlanken Gondeln passen schon 70 mm-Impeller, so dass hinreichend Schubleistung gewährleistet ist. So fiel dann die Entscheidung leicht, diesen Flugzeugtyp noch einmal als Bauprojekt in Angriff zu nehmen. In der Version 737-200 sah ich einen geeigneten Kandidaten für einen attraktiven Airliner mit überschaubaren Abmessungen. Die Variante 737-100 fiel bei mir durchs Raster. Sie ist etwas kürzer und damit noch pummeliger. Auch ist sie im Original in nur ganz geringen Stückzahlen von 30 Exemplaren gebaut worden.
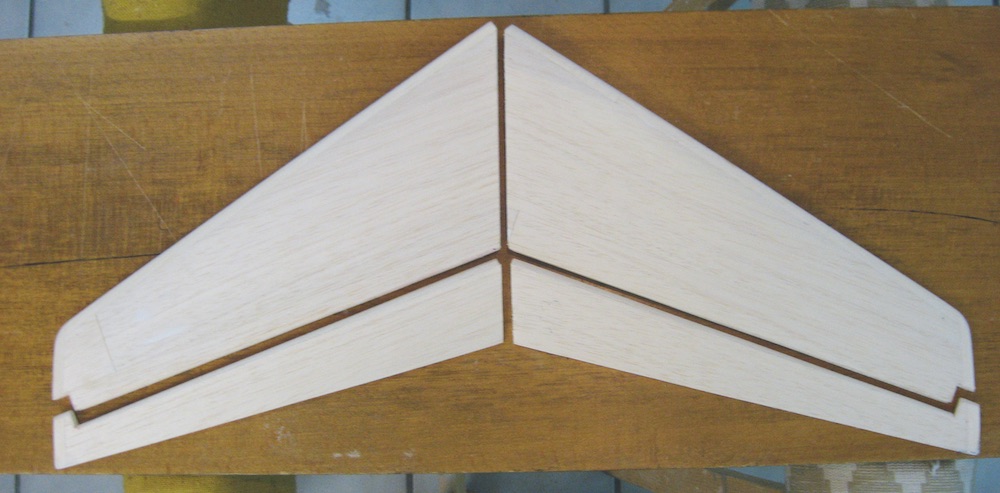
Rumpfheck und Leitwerk
Aus den vorhandenen Formen entstand zunächst ein GfK-Teilesatz mit Nase, Heck und Gondeln. Das Einkleben einer Endleiste aus 10 mm-Balsa sorgt für die nötige Torsionsfestigkeit des Seitenleitwerks. Das Höhenleitwerk wird mit dem heißen Draht aus Styropor geschnitten und in der üblichen Weise mit 1 mm-Balsa beplankt. Nach Anbringen von Nasenleiste und Randbogen können die Leitwerkshälften verschliffen werden. Die Höhenruder werden abgetrennt. Auf die Trennkante der Ruder wird 5 mm-Balsa geklebt und rund verschliffen. Gleichzeitig wird aus den Leitwerken eine Hohlkehle ausgeschliffen und mit 80 g-Glasgewebe verschlossen. Nun können die Leitwerkshälften mit 7° V-Form zusammengeklebt werden. Im Rumpfheck werden die notwendigen Ausschnitte vorgenommen und das fertige Höhenleitwerk eingeklebt. Zwischenzeitlich entsteht das Seitenruder als Balsakonstruktion, so dass die komplette Heckpartie vorläufig beiseite gestellt werden kann.
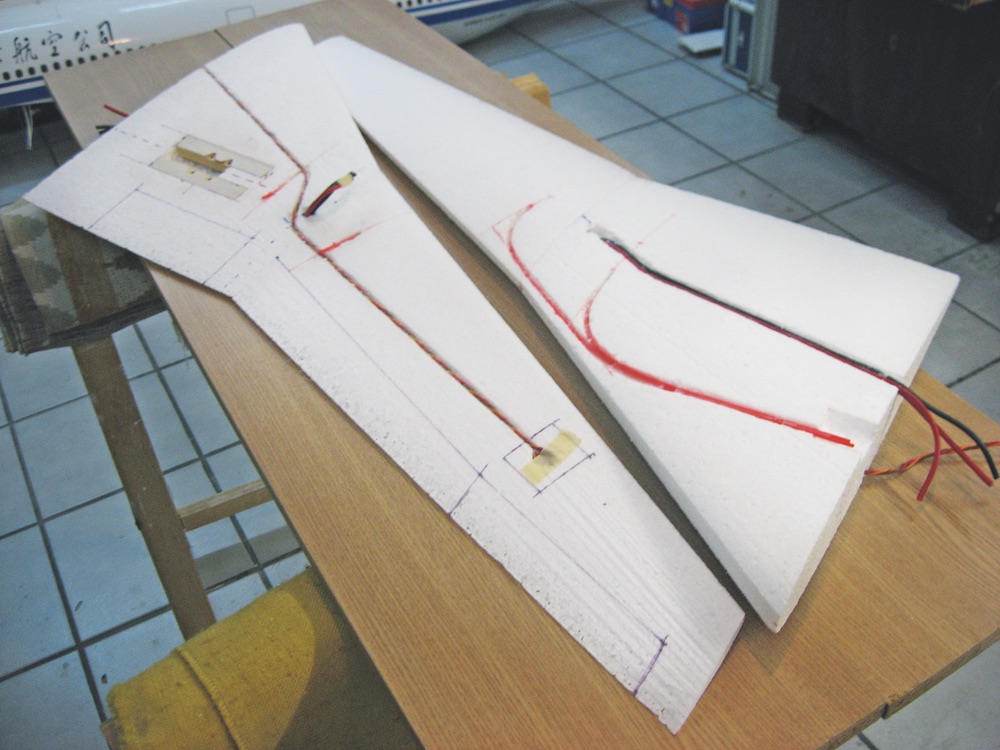
Tragflächen
Auch hier werden zunächst die Kerne geschnitten. Jede Flügelhälfte besteht aus zwei Teilen, die stumpf zusammengeklebt werden. Wichtig ist, dass das Wurzelprofil schon in derselben Anstellung zum Styroporblock geschnitten wird, die es später auch zum Rumpf haben soll. Das erleichtert später das korrekte Ausschneiden der Flügelaufnahme im Rumpf. Vor dem Beplanken werden die Fahrwerksträger (19 x 12-mm Kiefernleisten), die elektrischen Zuleitungen für die Querruderservos und die Bowdenzugrohre zur Anlenkung der Landeklappen verlegt. Letztere werden später durch ein einzelnes Servo in der Flügelmitte betätigt. Alles wird verspachtelt und verschliffen, gefolgt vom Beplanken mit 1 mm-Balsa. Nach dem Anbringen von Nasenleiste und Randbogen steht das Verschleifen der Flügel an. Landeklappen und Querruder werden ausgeschnitten, verkastet und verschliffen, die Hohlkehlen am Flügel mit Glasgewebe verschlossen. Jetzt sind die Flügelhälften so weit fertig, dass sie mit 6° V-Form miteinander verklebt werden können. Die Flügelmitte durch eine Lage Glasgewebe an Ober- und Unterseite verstärkt. Damit ist auch dieser Bauabschnitt abgeschlossen.
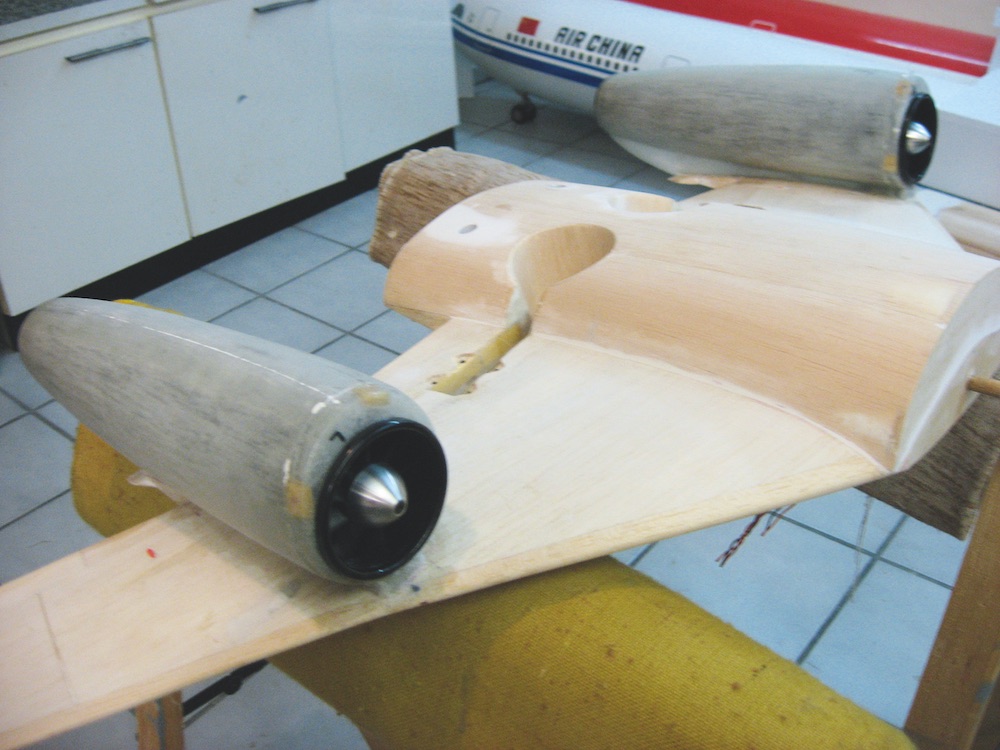
Rumpfnase und Mittelrumpf
Aus leichtem Sperrholz wird eine Halterung für die Bugfahrwerksmechanik gebaut und mit Kohlefaser verstärkt. Verschraubt wird diese dann mit einem in der Rumpfnase eingeklebten Halbspant. Nun geht es an den Mittelrumpf. Dazu werden zunächst die entsprechenden Halbschalen aus Styropor geschnitten. Zum Aufbringen der 1 mm-Balsabeplankung werden Balsaholz und Styropor mit leicht wasserverdünntem Weißleim bestrichen. Nach dem Abtrocknen kann die Beplankung aufgebügelt werden. Nächster Arbeitsgang ist das Zusammenkleben der der beiden Halbschalen zur Rumpfröhre. Um den Flügelausschnitt im Rumpf herzustellen, wird schrittweise …